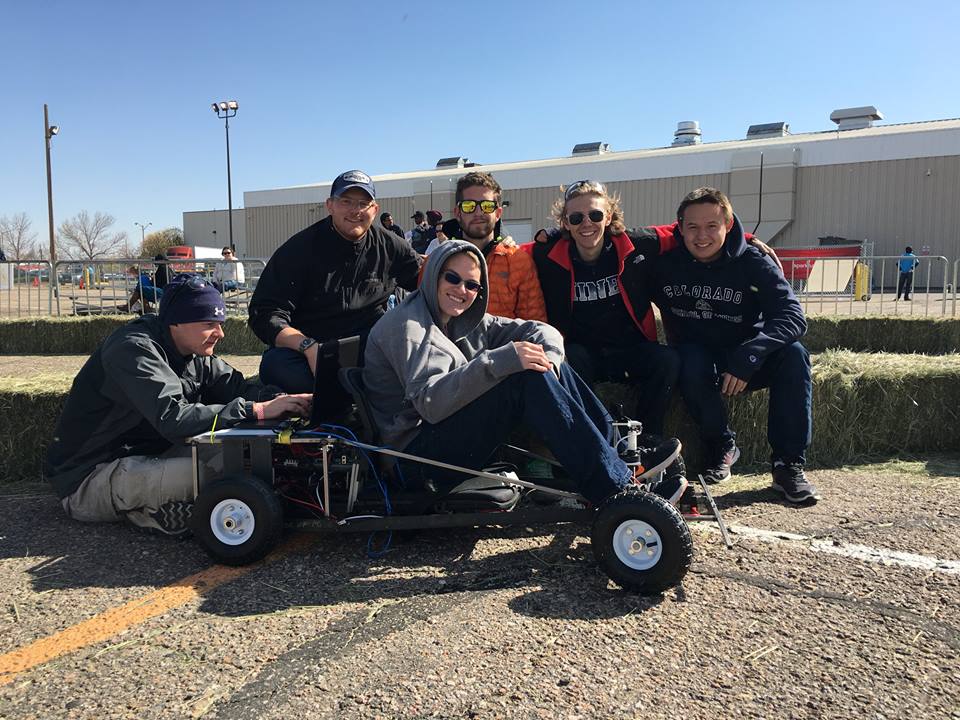
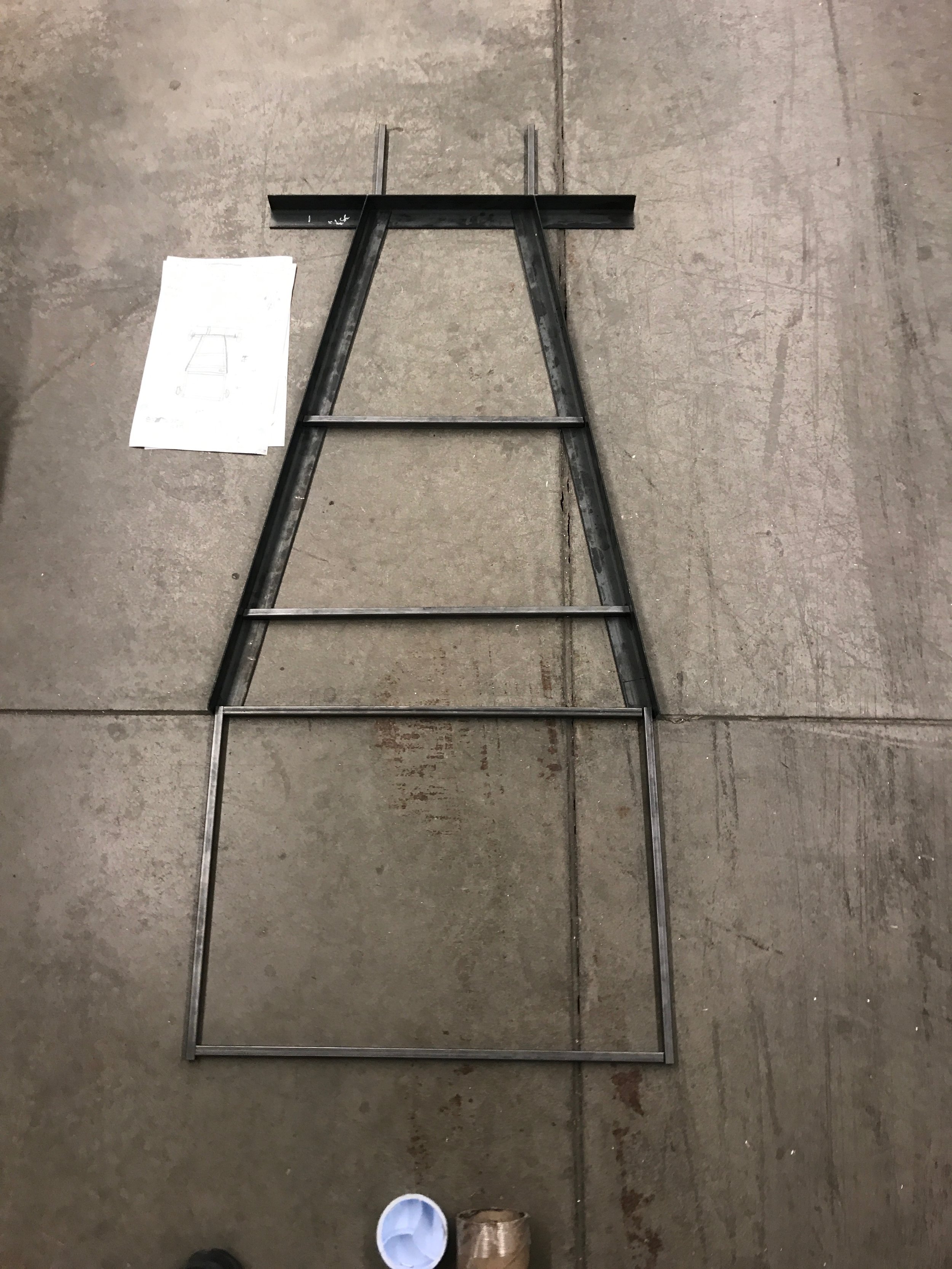
The team, lead by Sevy, started out by designing a frame and cutting out all the correct lengths of steel. Shown in the picture is the metal laid out in the orientation it will be welded. A picture of the design is in the upper left.
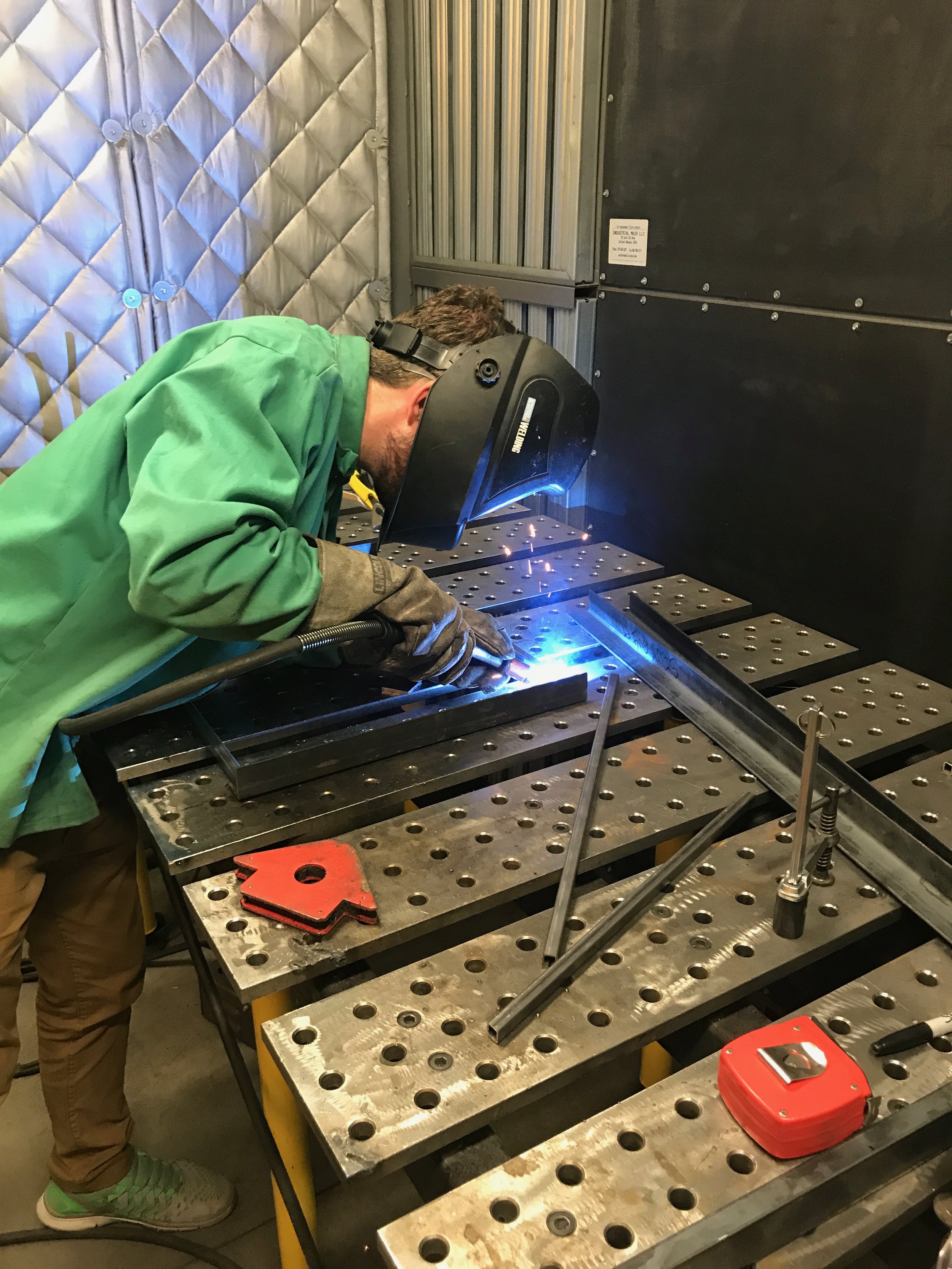
The welding process starts.
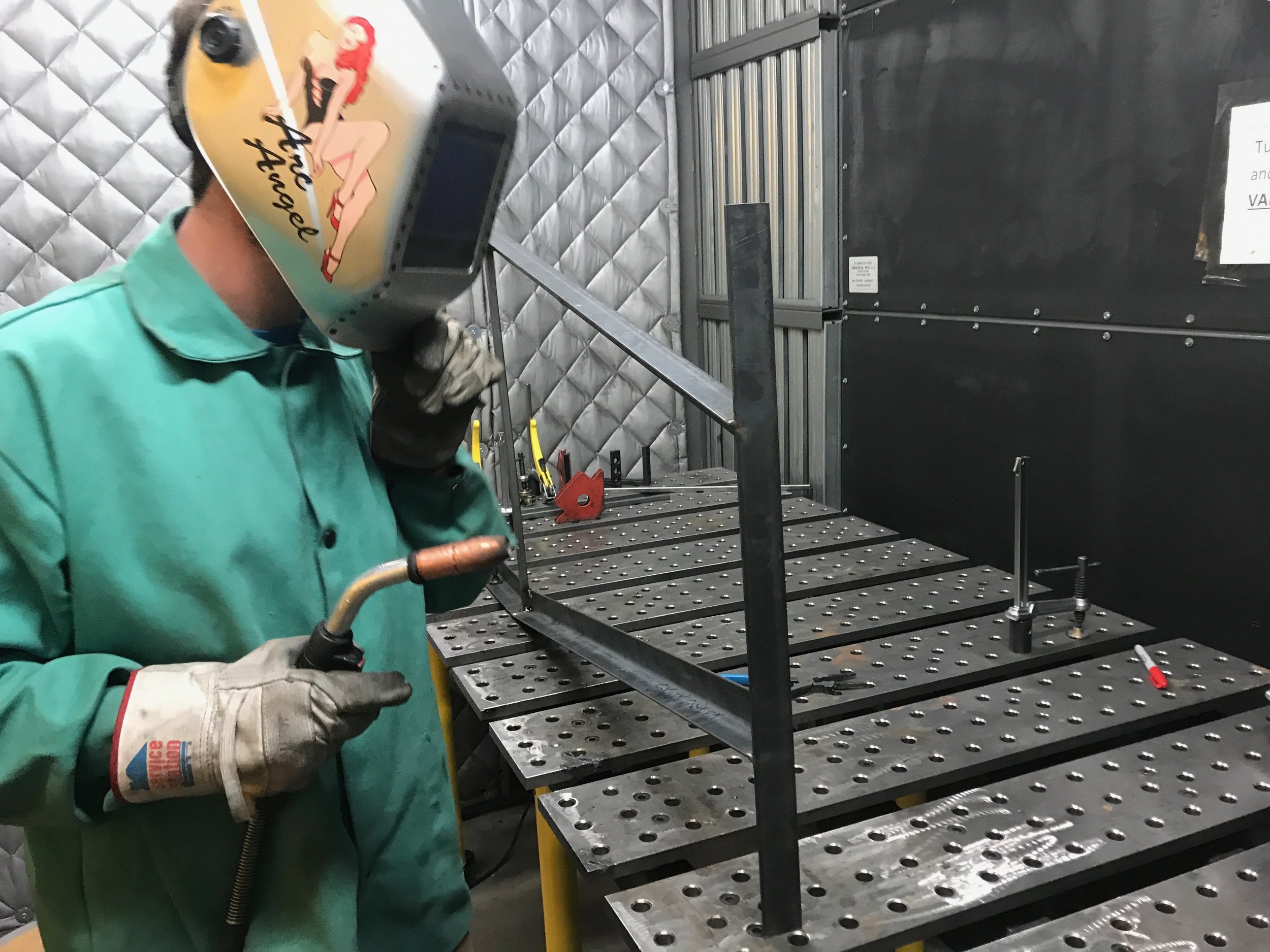
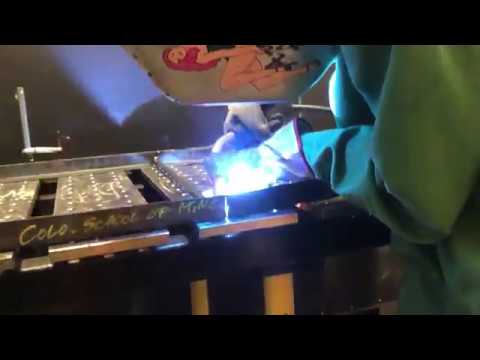
The mostly finished frame.
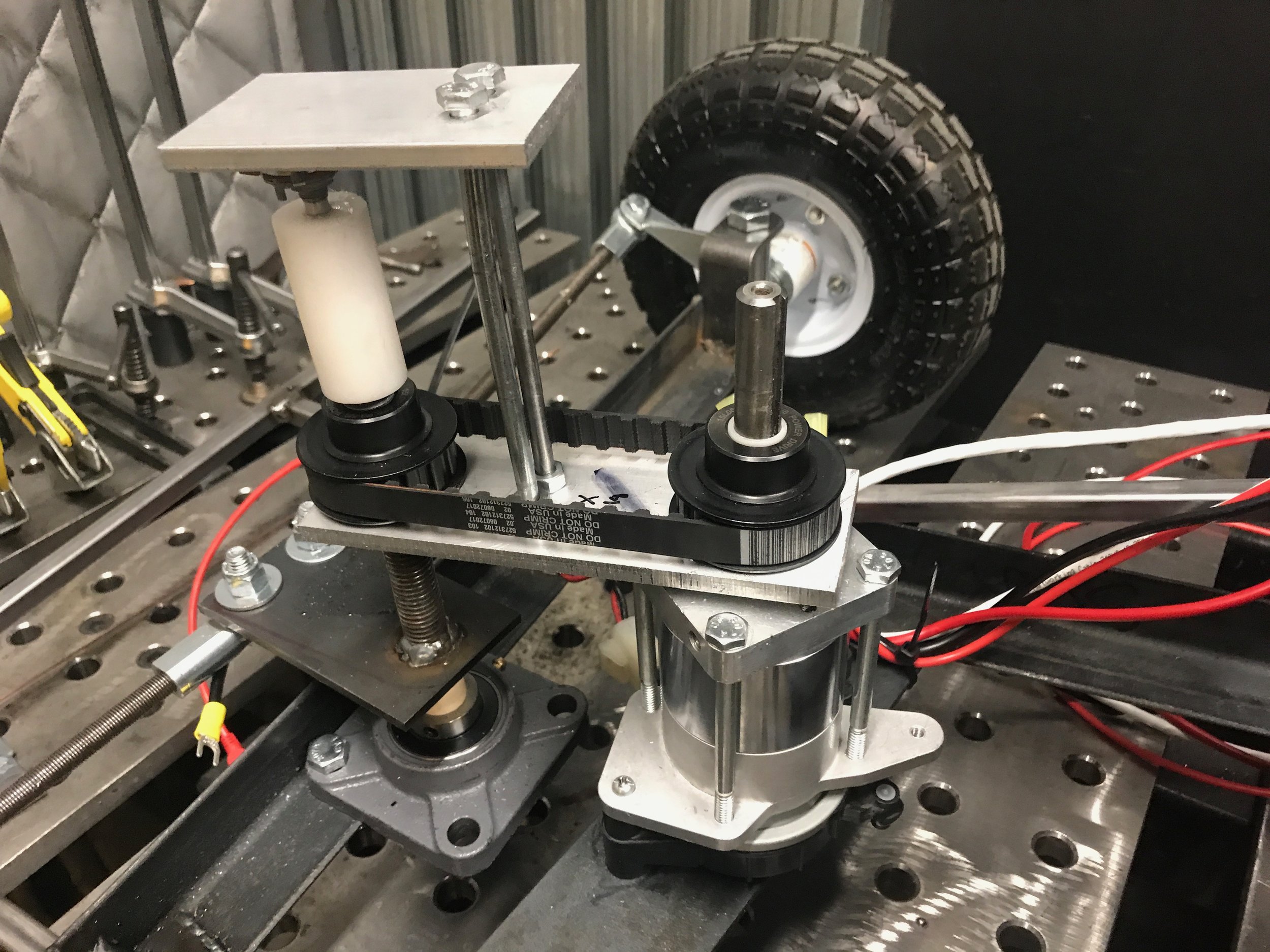
The steering mechanism: The particular sub-system above took a week to put together. A problem the team solved along the way was the motor did not have enough torque to steer the wheels. They added a planetary 12:1 gearbox on top to give it less speed and more strength to overcome this problem.
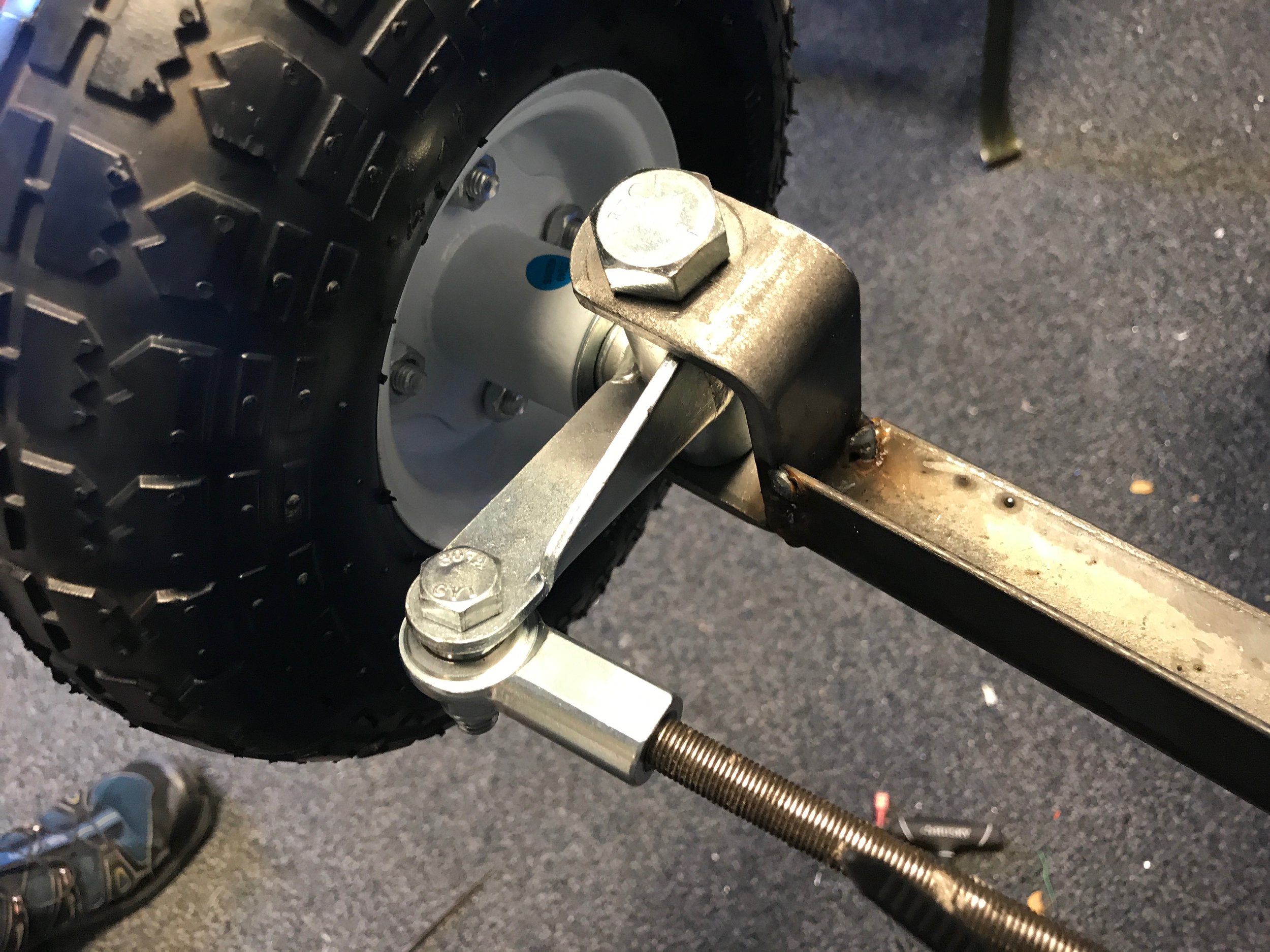
A steering arm and wheel are attached to a spindle that rotates on a bracket welded to the frame.
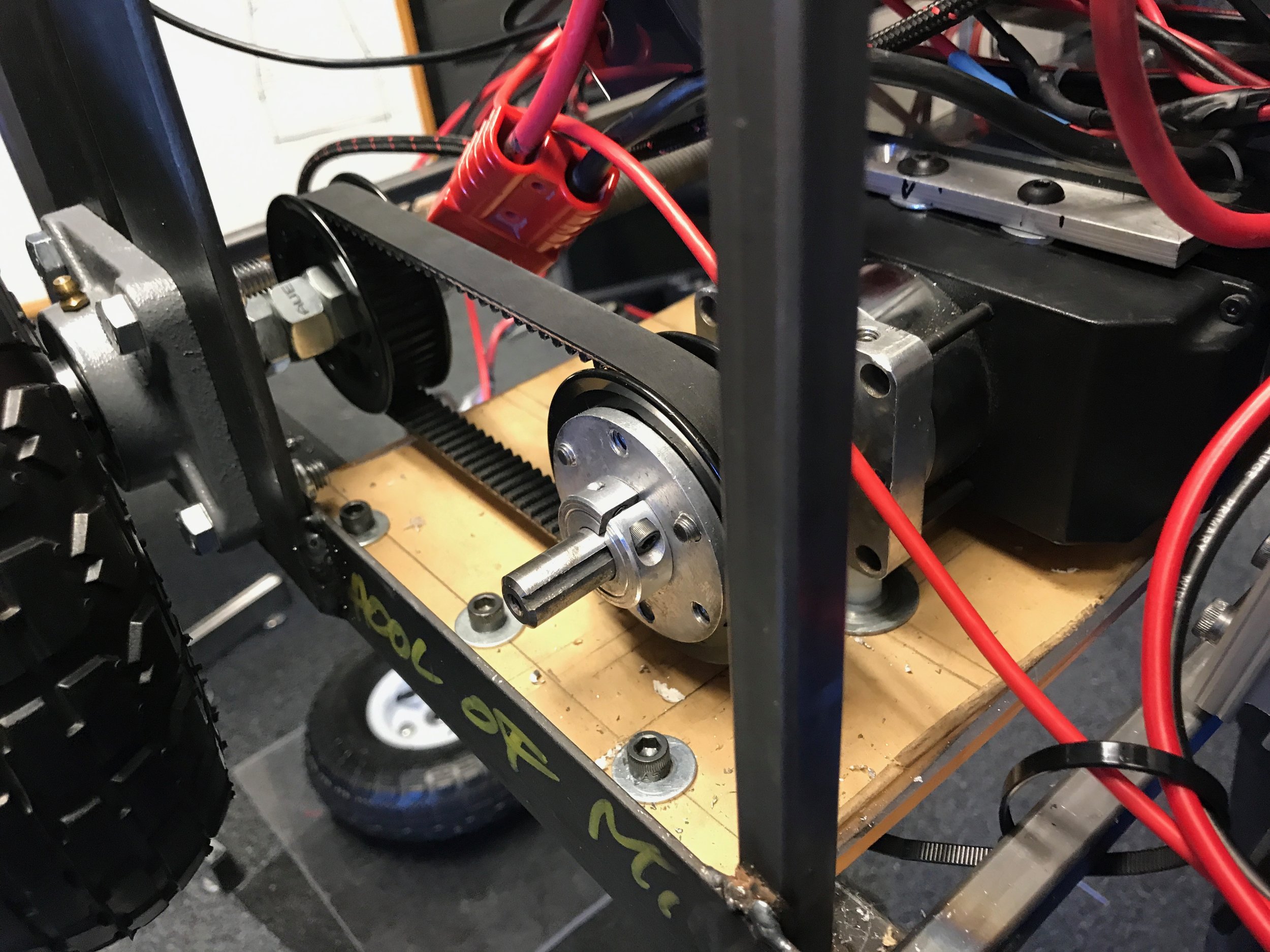
This was the initial drive train system. It consisted of a timing belt connecting a motor gearbox to a main drive shaft.
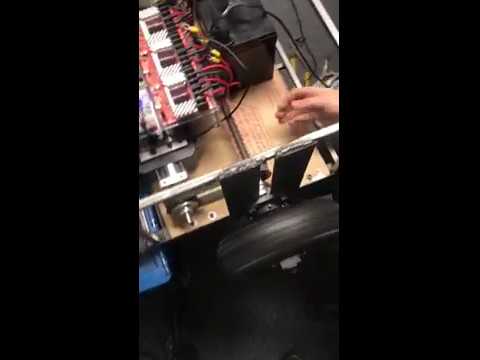
Sevy is running the motor and applying resistance to the wheel to simulate it on the ground. He does not like the sound it is making. Also notice how the motor wobbles. That is also a big problem.
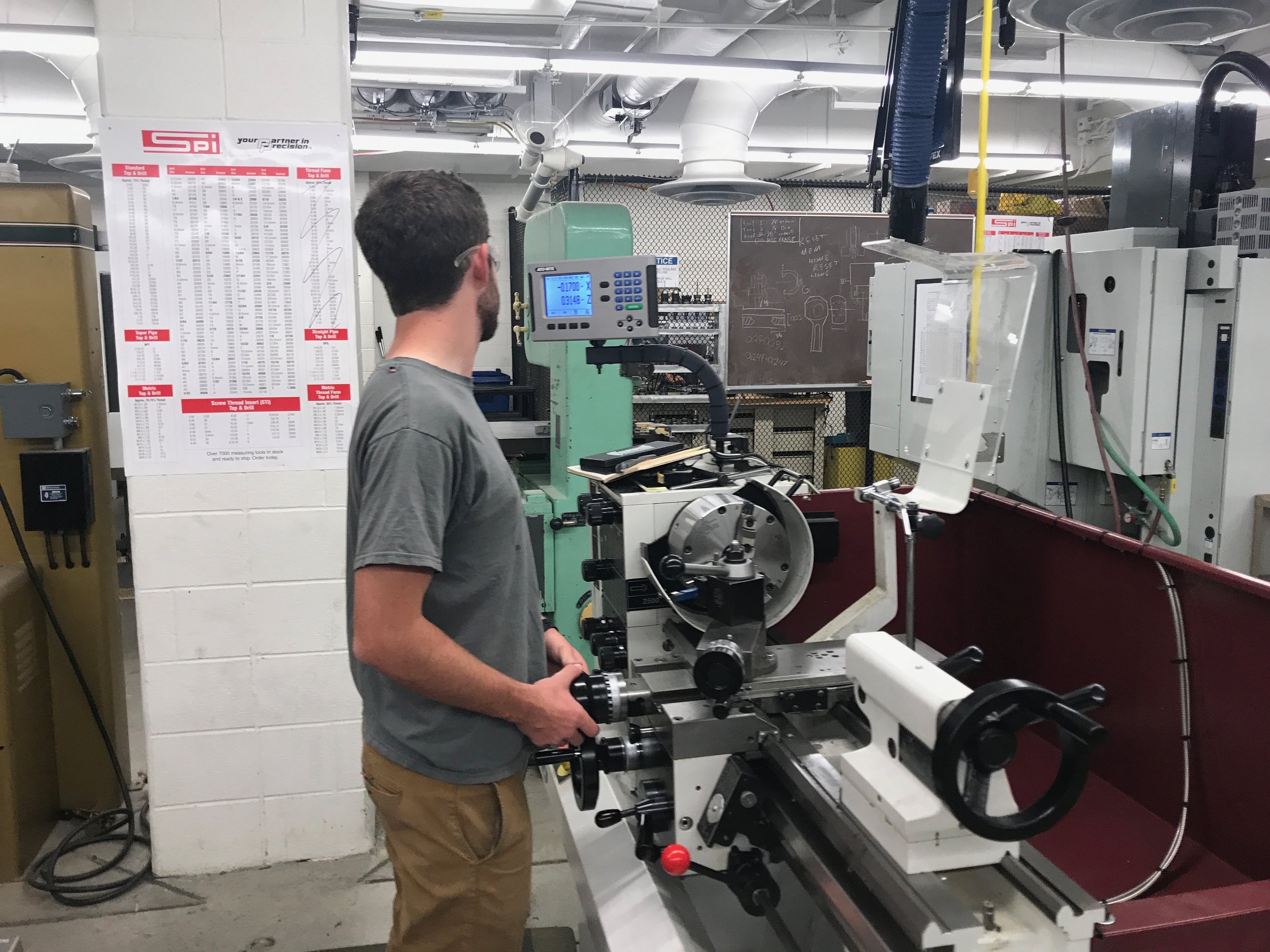
At this point the team decided to do direct drive from the motors to the wheels and bypass the timing pulleys and belts. This is one member of the team turning a part on the lathe that will become a spacer between the drive shaft and the main bearing attached to the frame (pillow block). Normally one never goes directly from motor to wheel (direct drive) but the robot was due at competition the following day. Everyone agreed the direct drive would be the most likely to function.
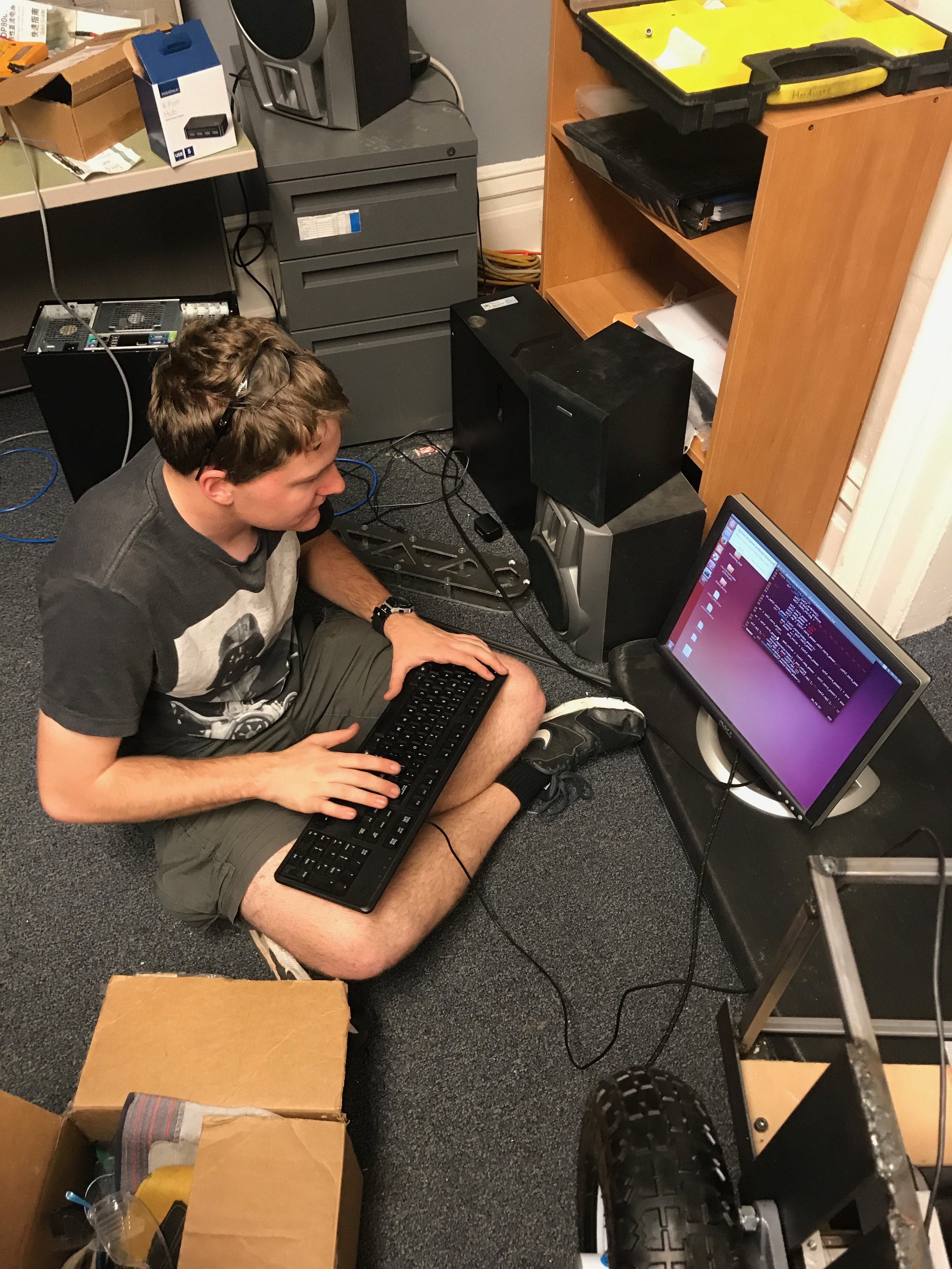
In this shot, one member of the team is programing the autonomy code that will be later used to control the wheels and steering.
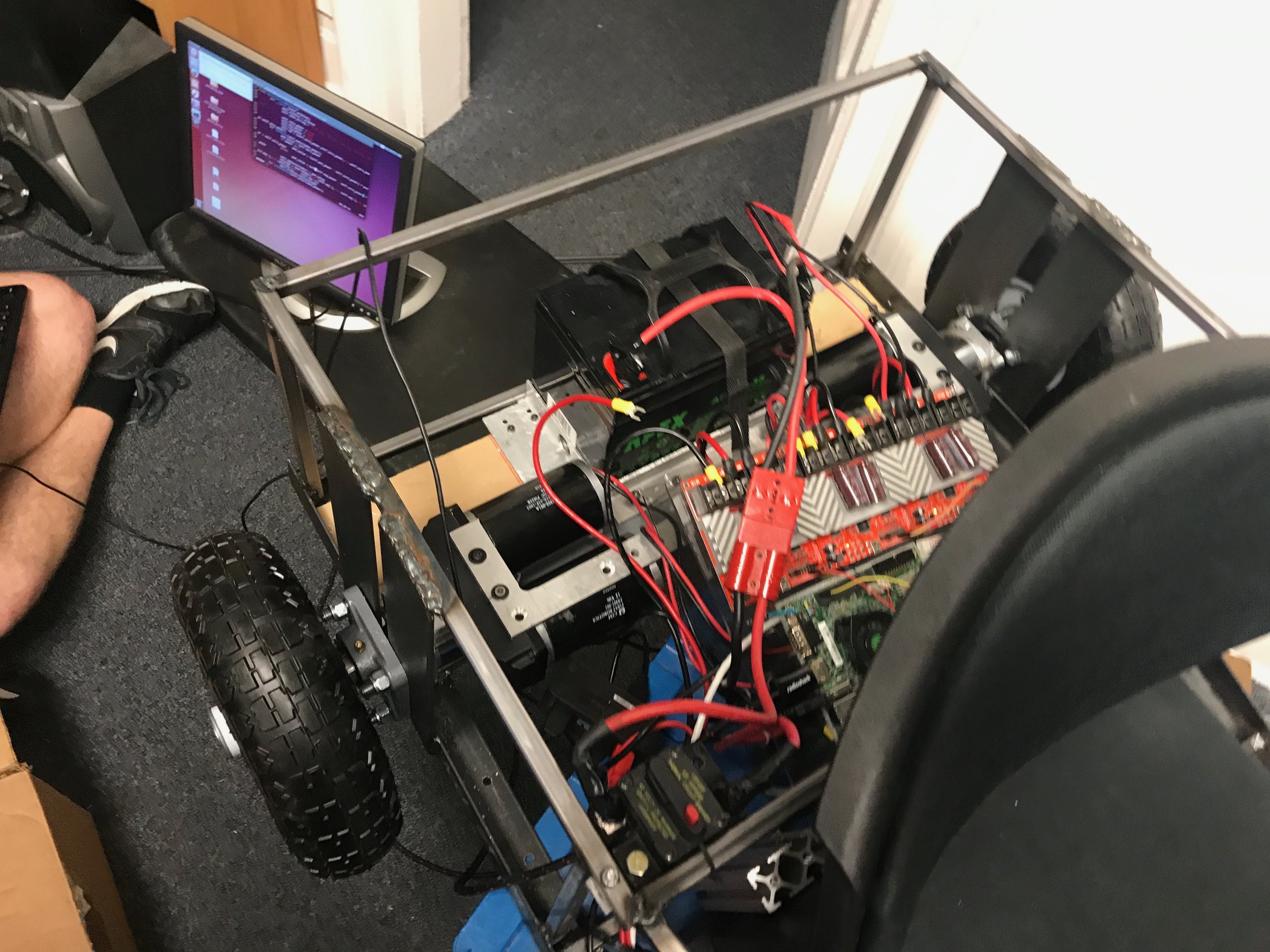
Direct drive! Amazingly, it functions.
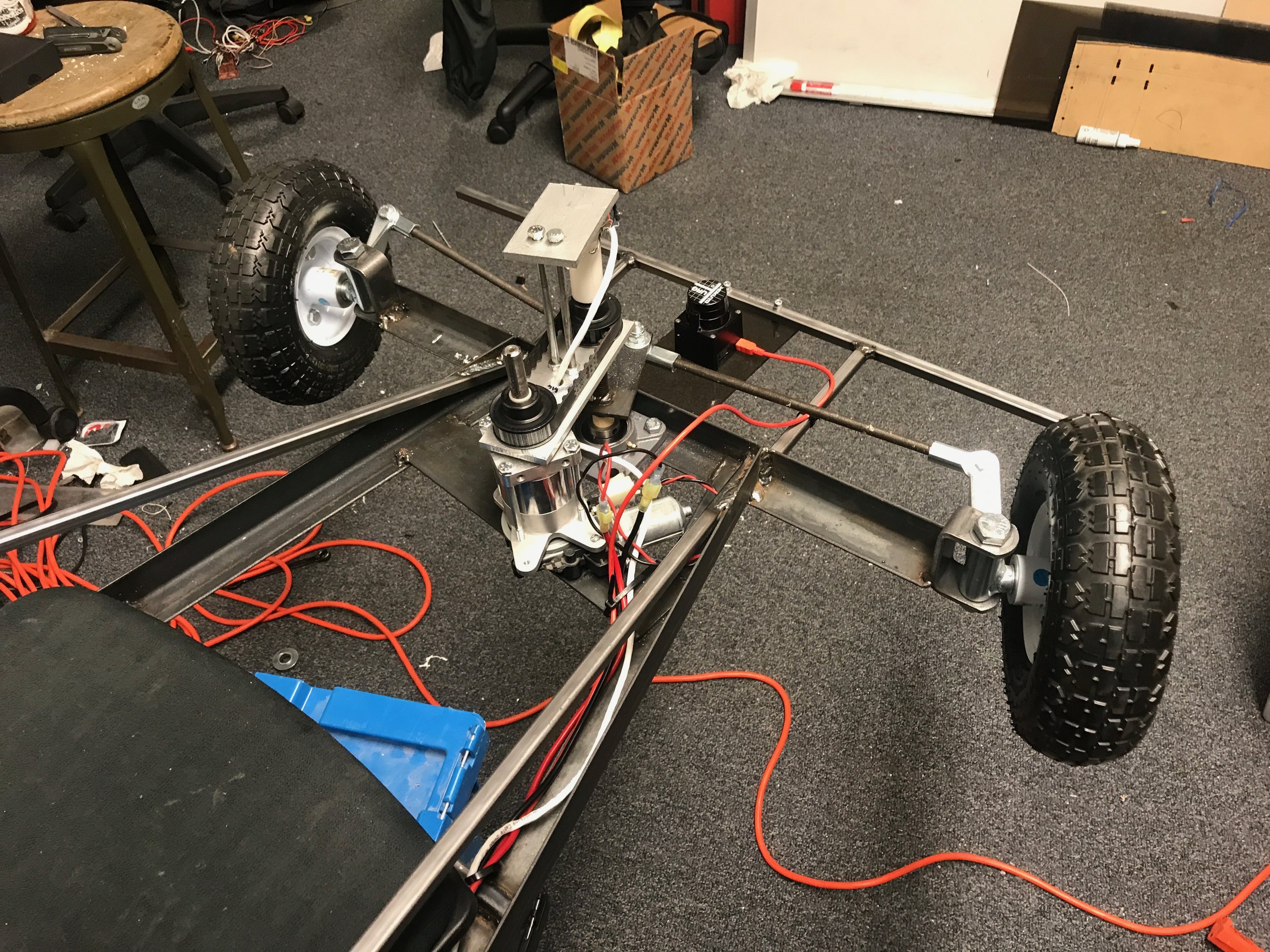
The steering sub-system is all wired up.
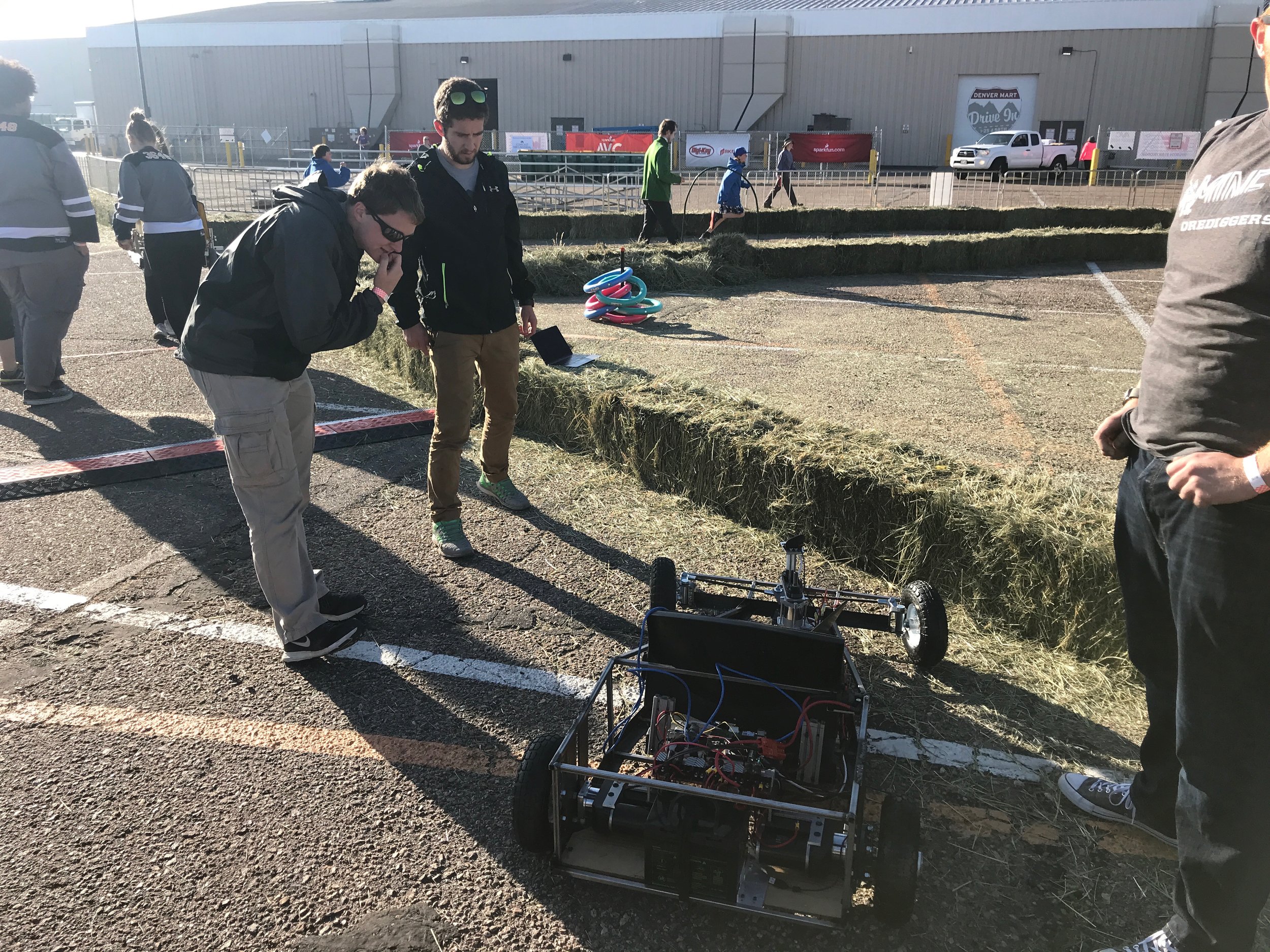
Testing out autonomous code at the competition. The team used LIDAR as their main sensing apparatus. It could look forward and identify the direction and distance of the hay-bails.
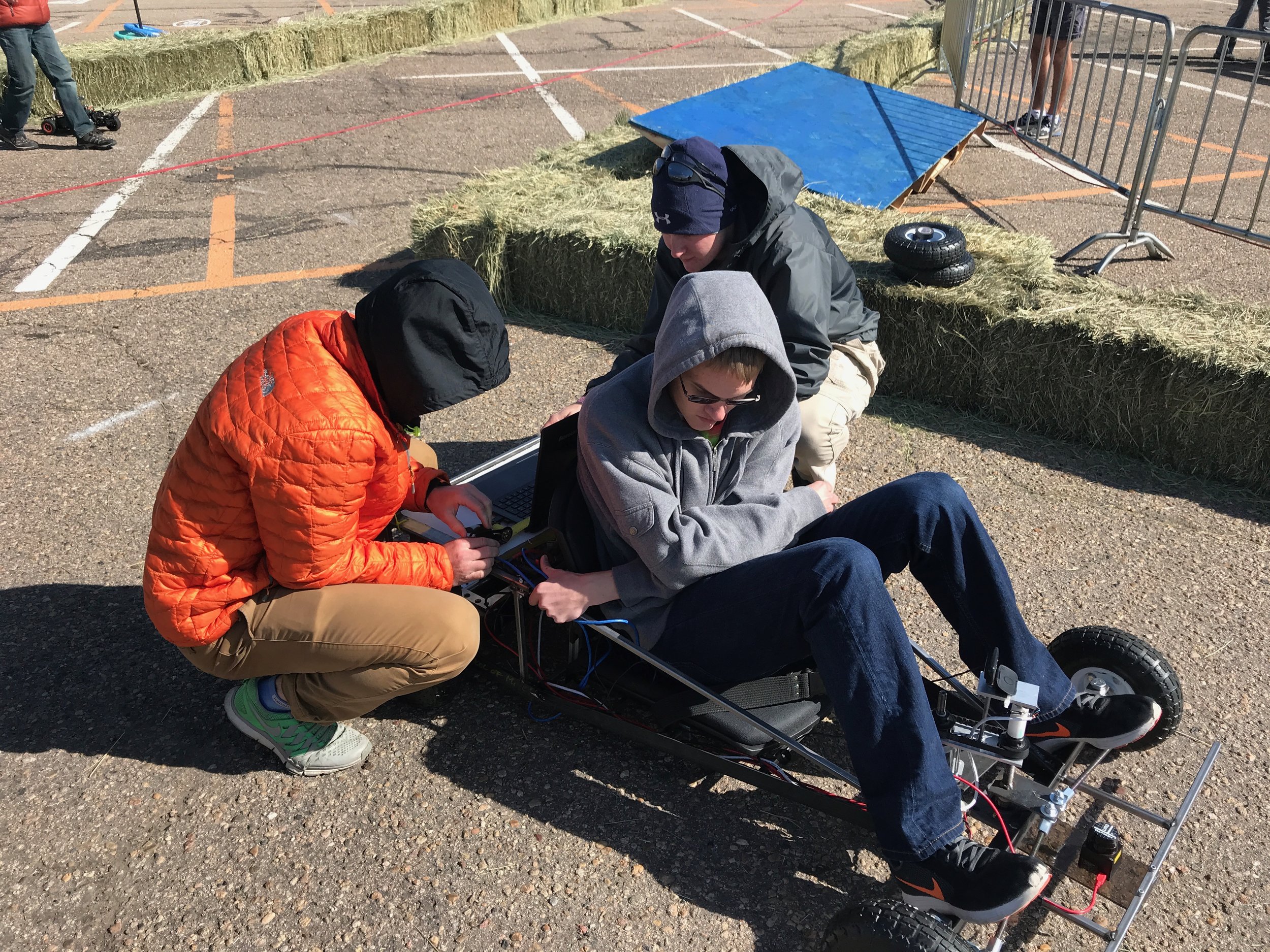
Making some last minute touches before the AVC Sparkfun Autonomous Car Wars Competition.
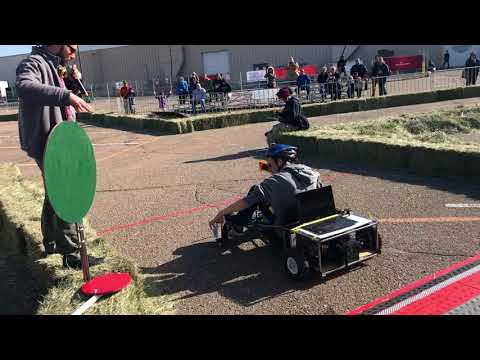
The car successfully runs and steers with a person riding it after only seven weeks. However, the autonomous code as you see above needs some more time and labor. Overall the team and Sevy learned a great deal from mechanical car subsystems to time management at the extreme.
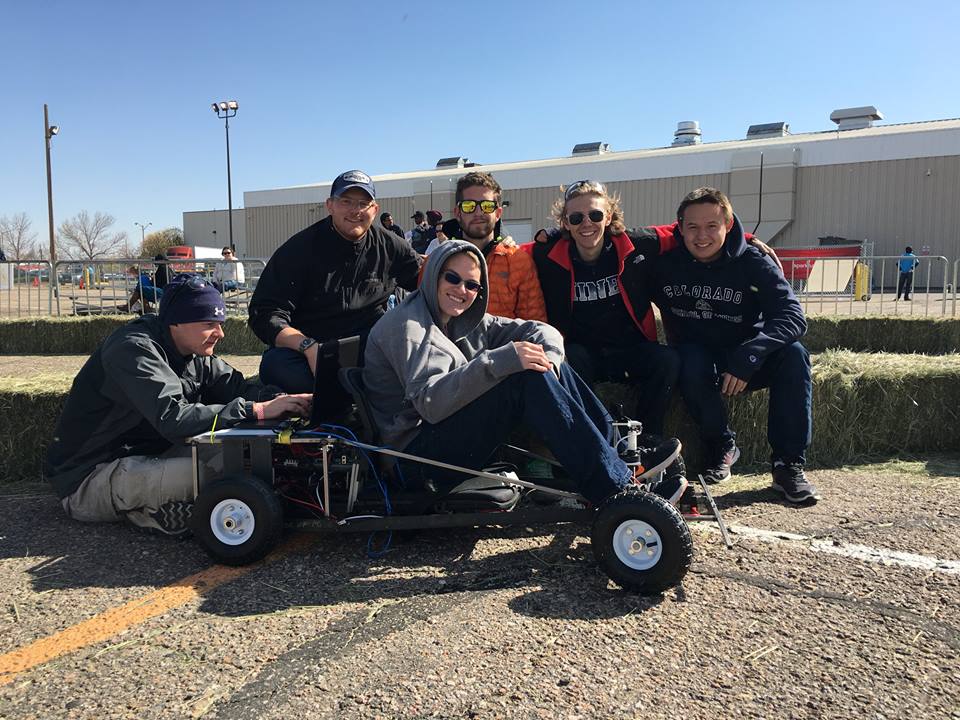
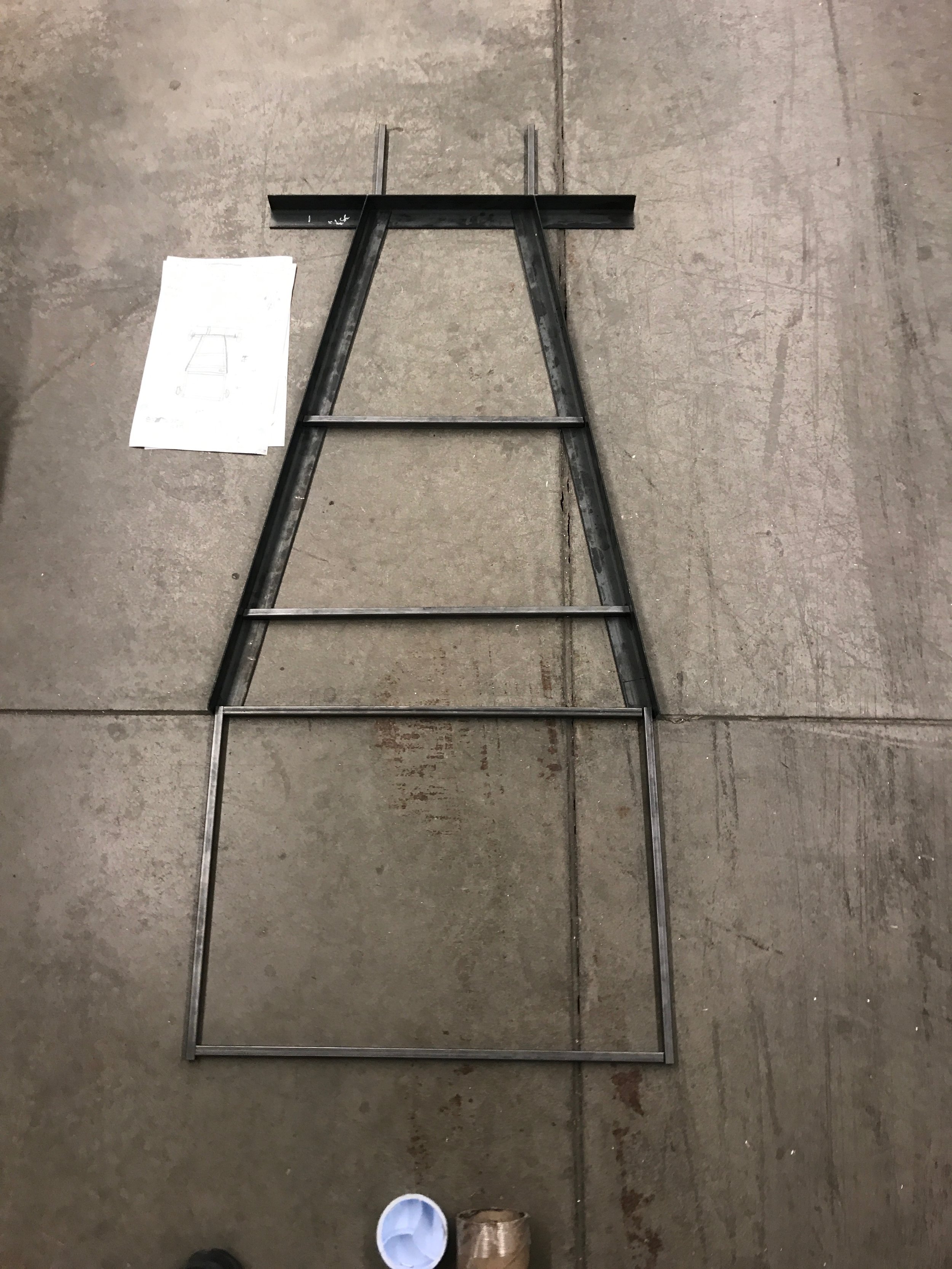
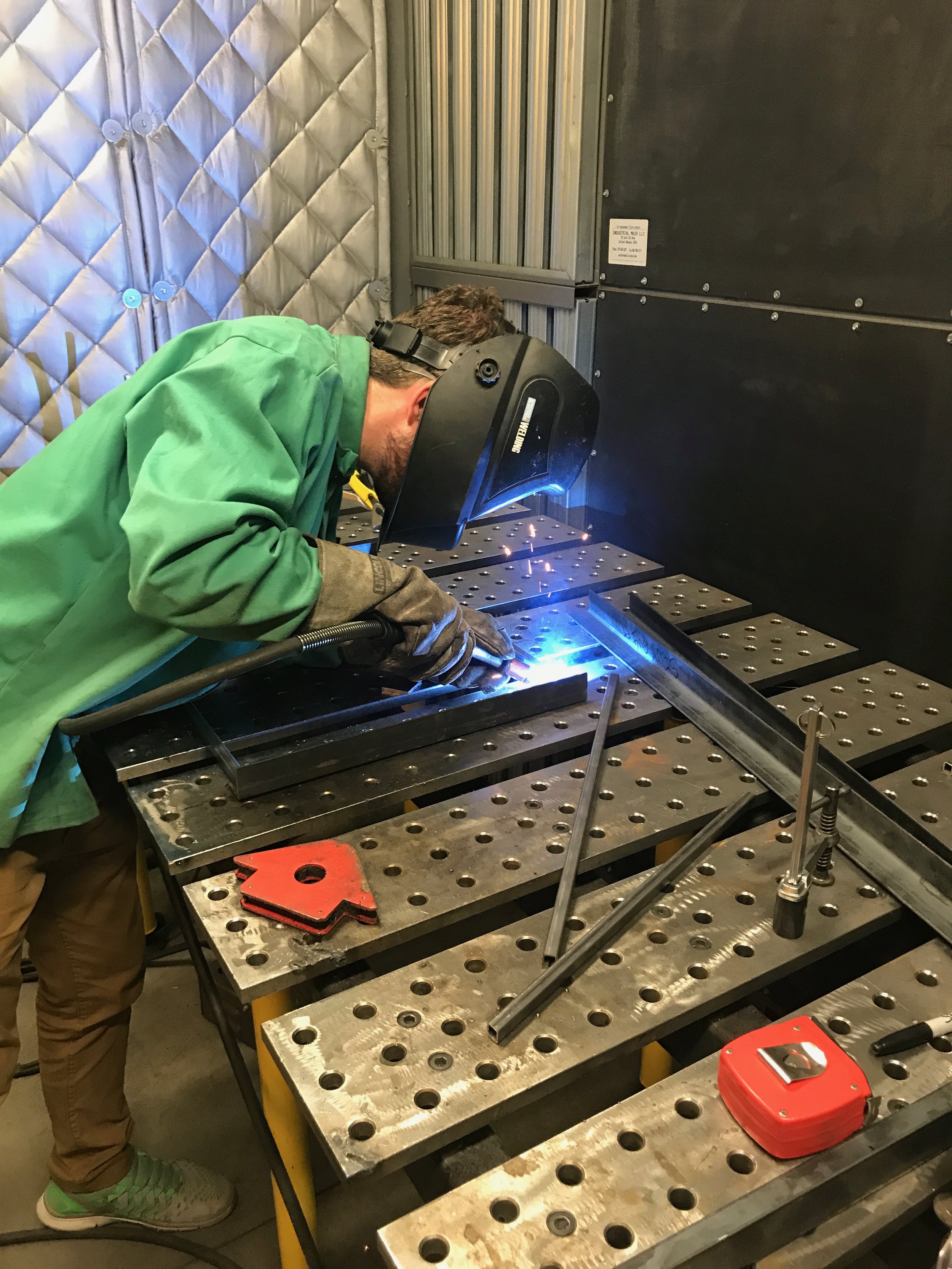
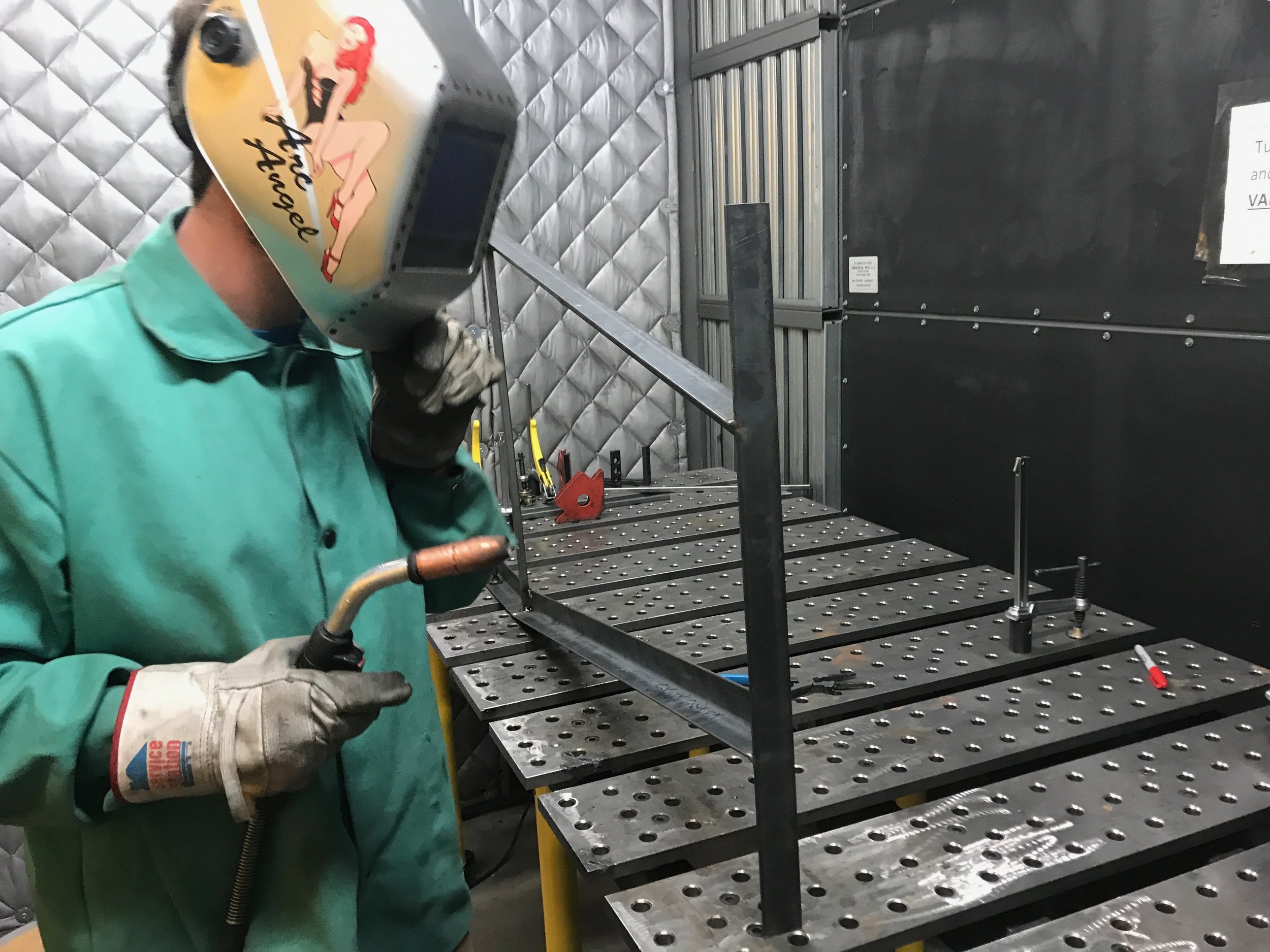
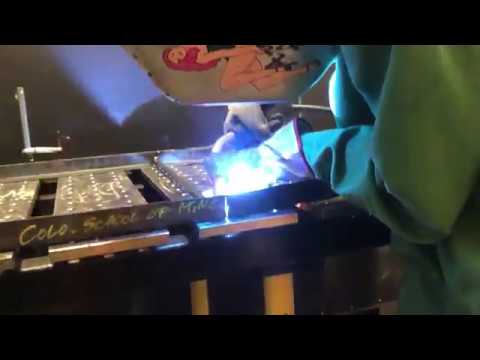
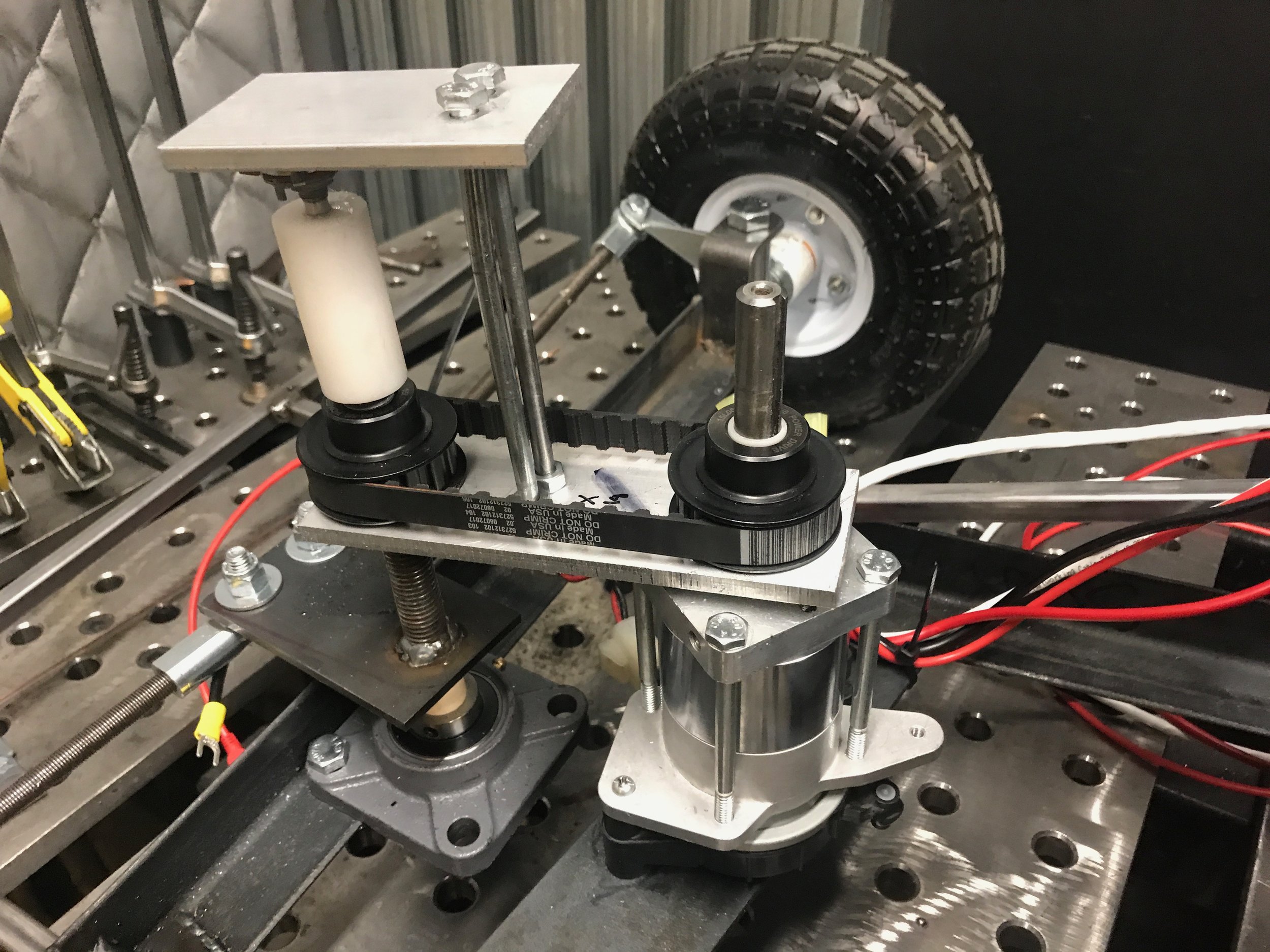
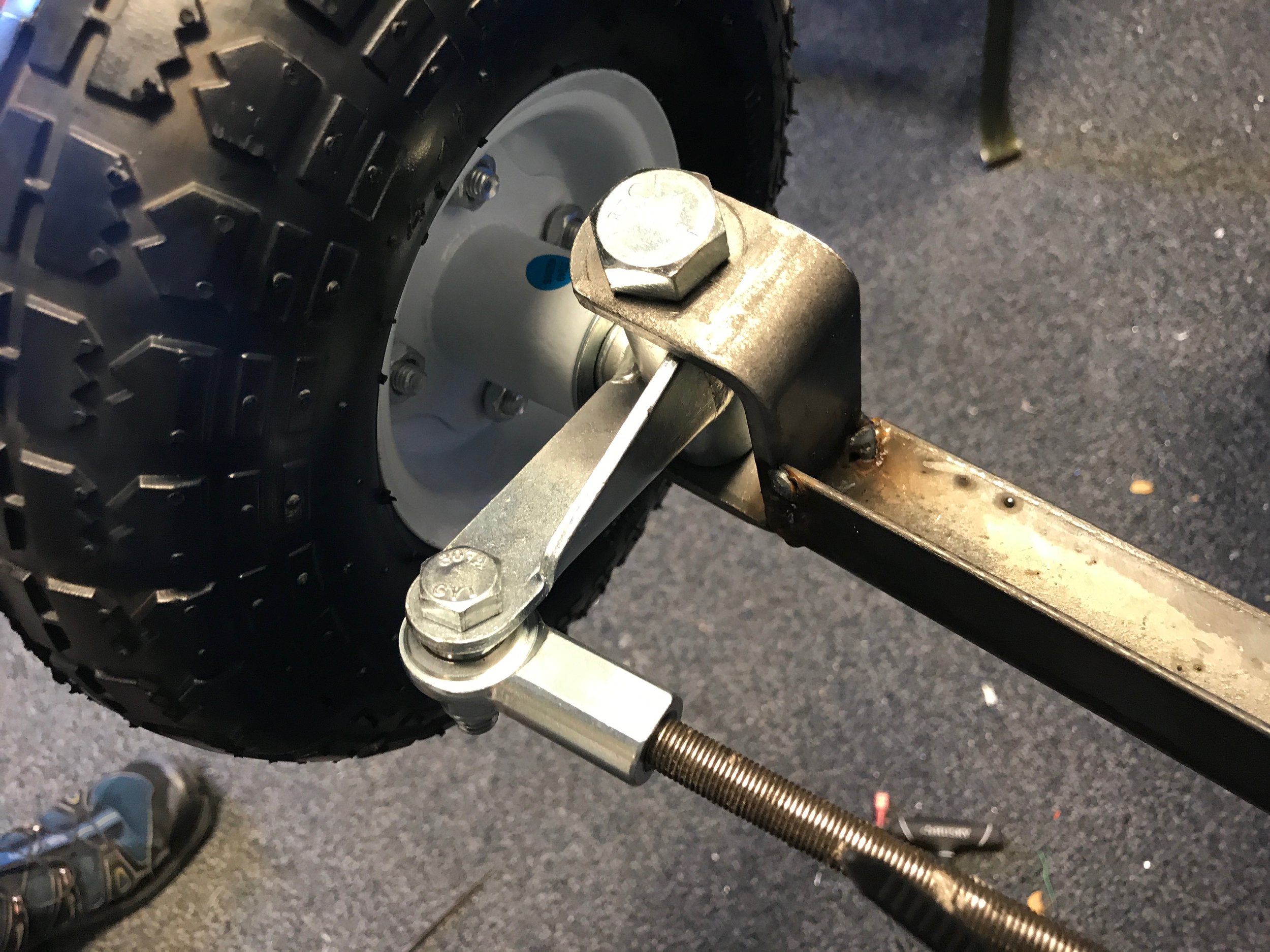
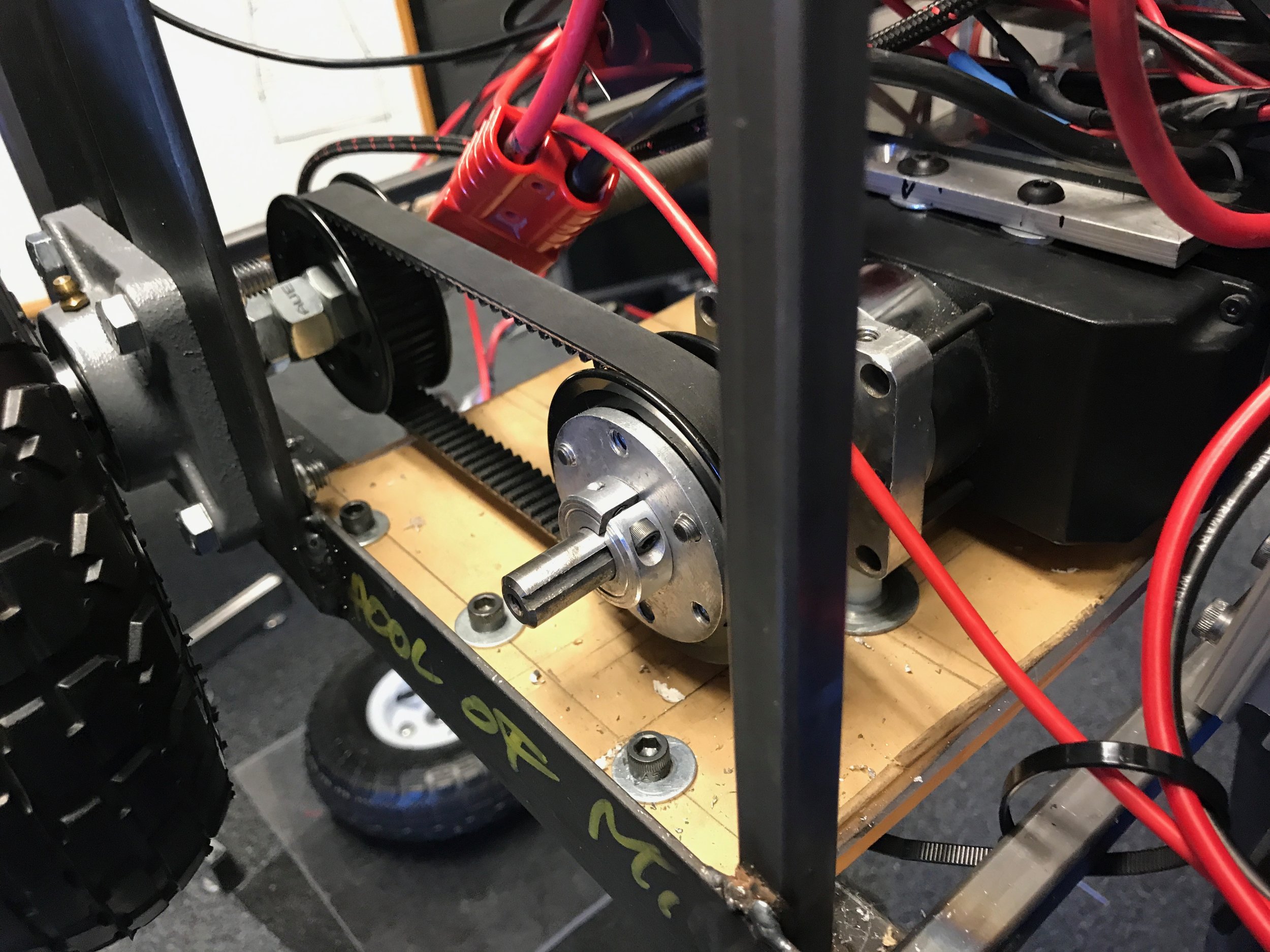
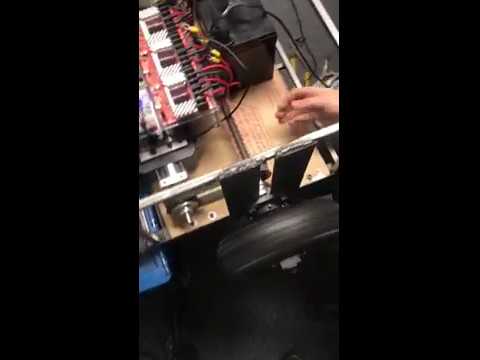
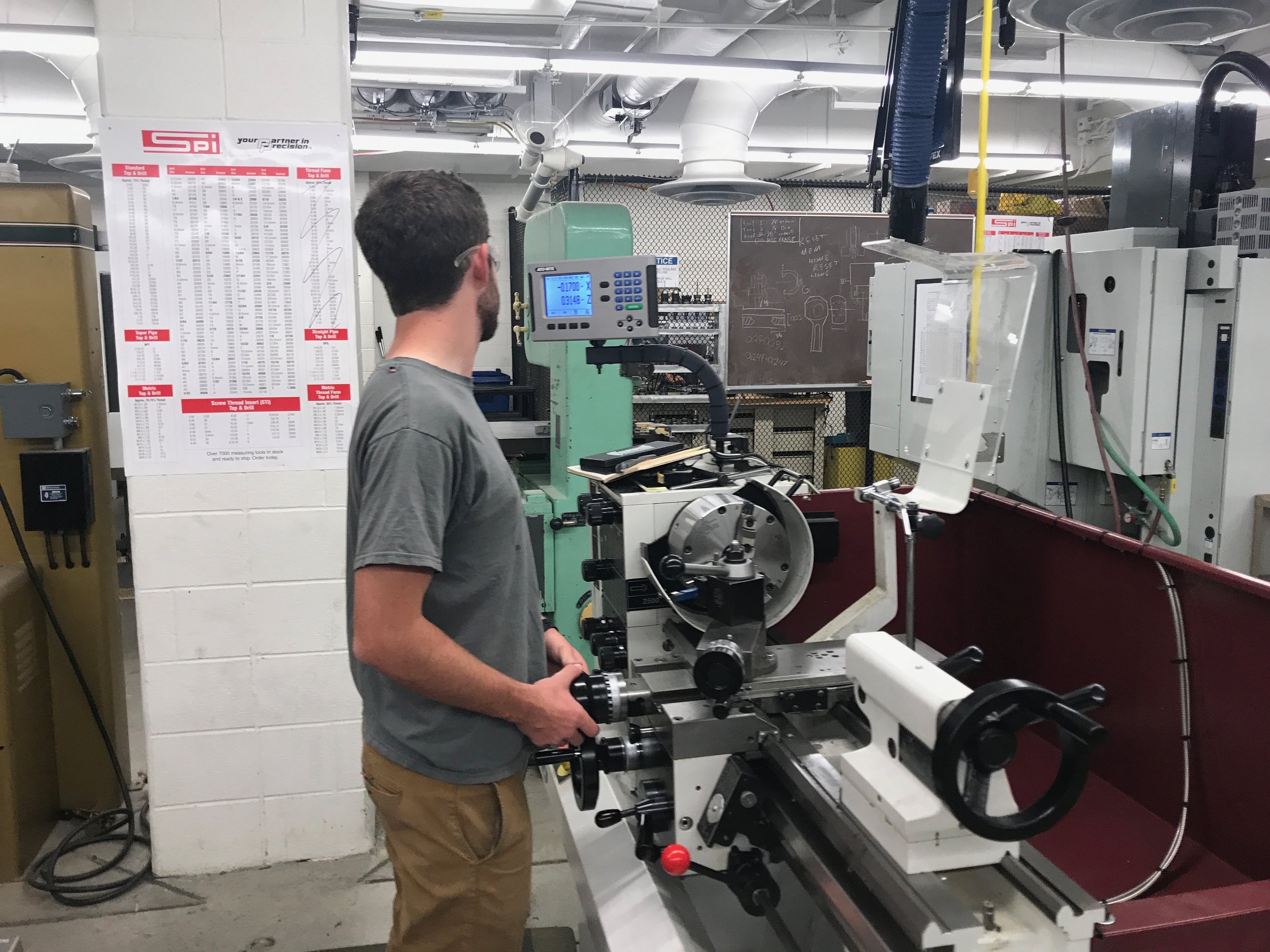
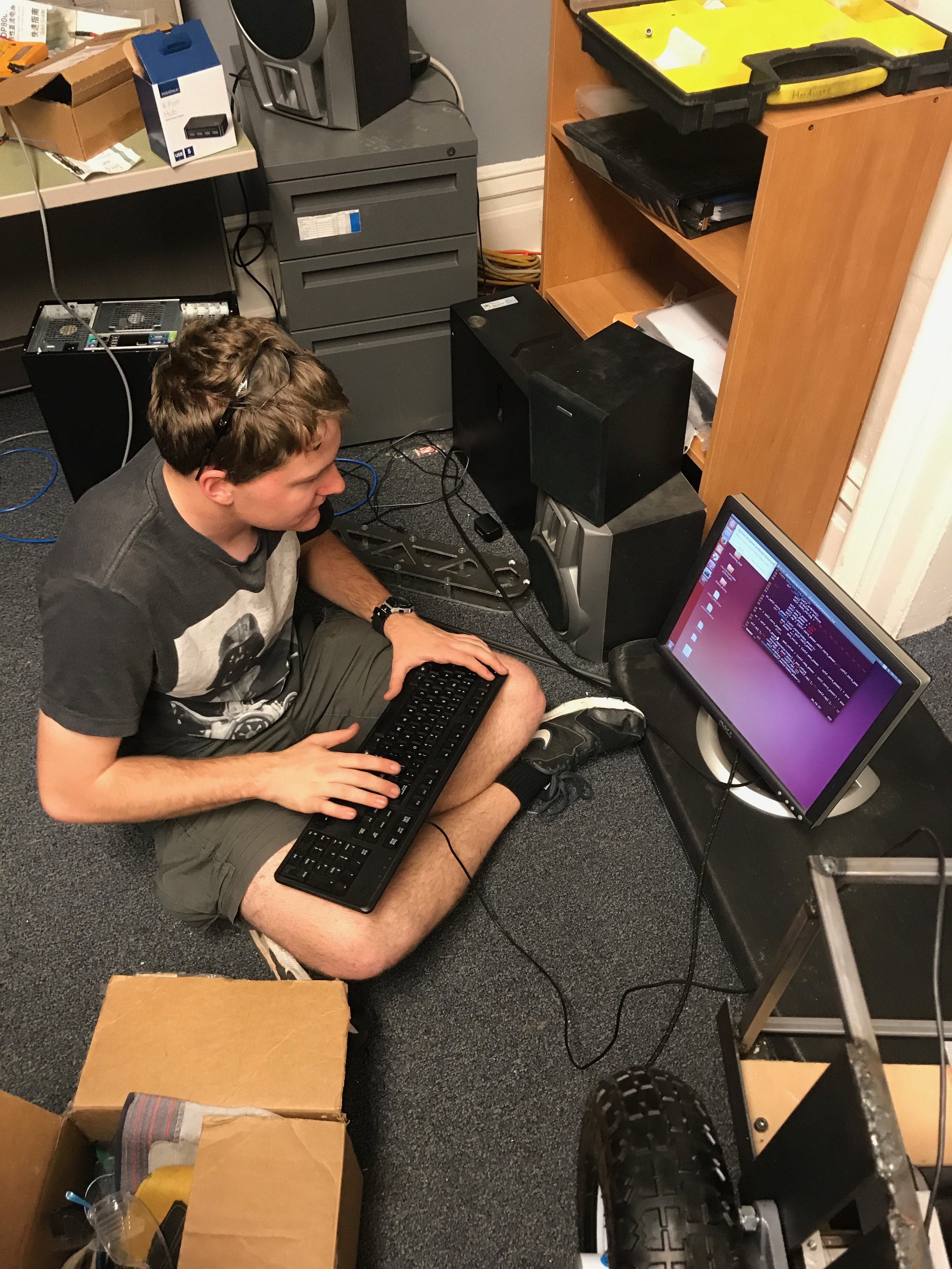
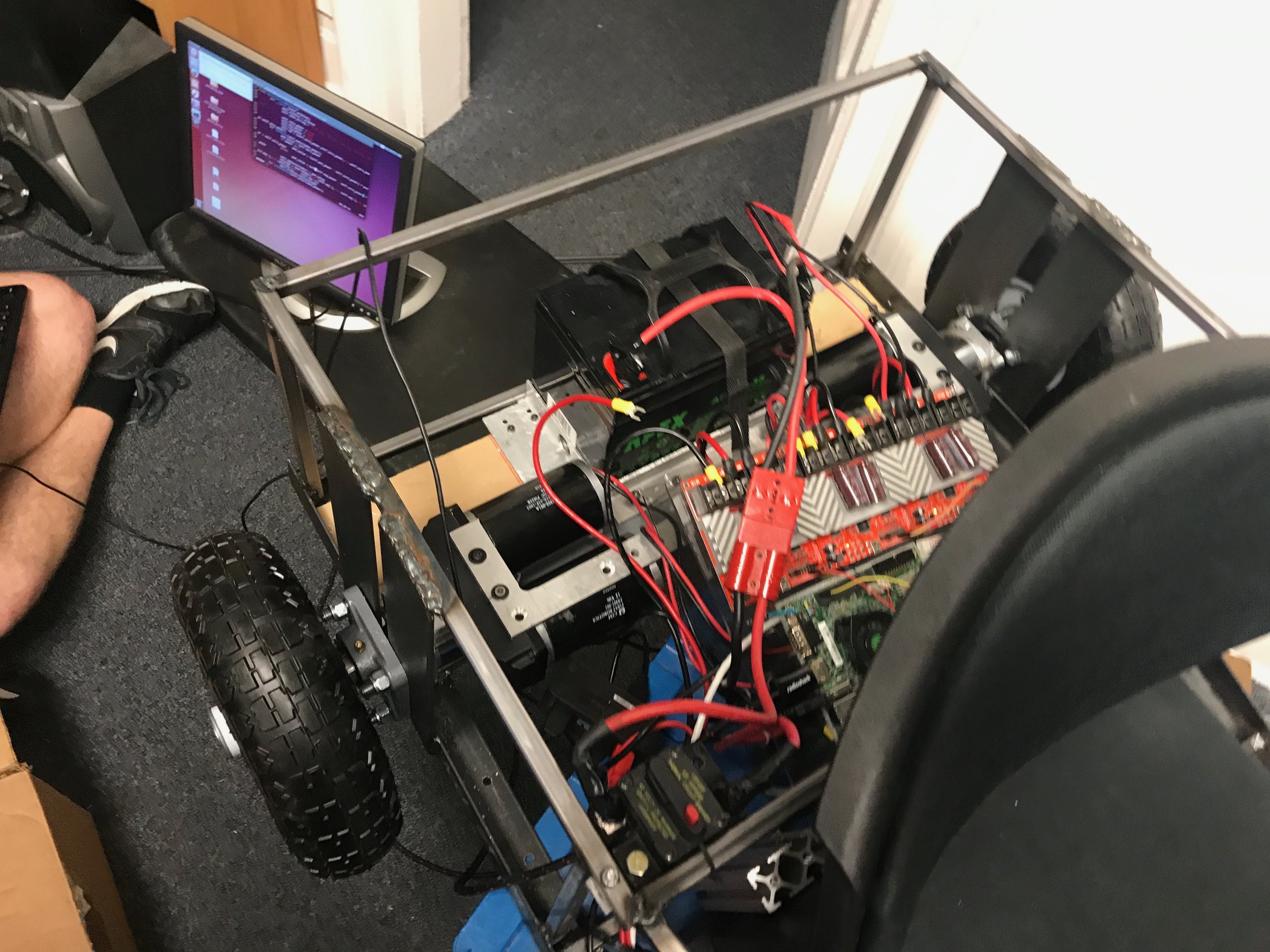
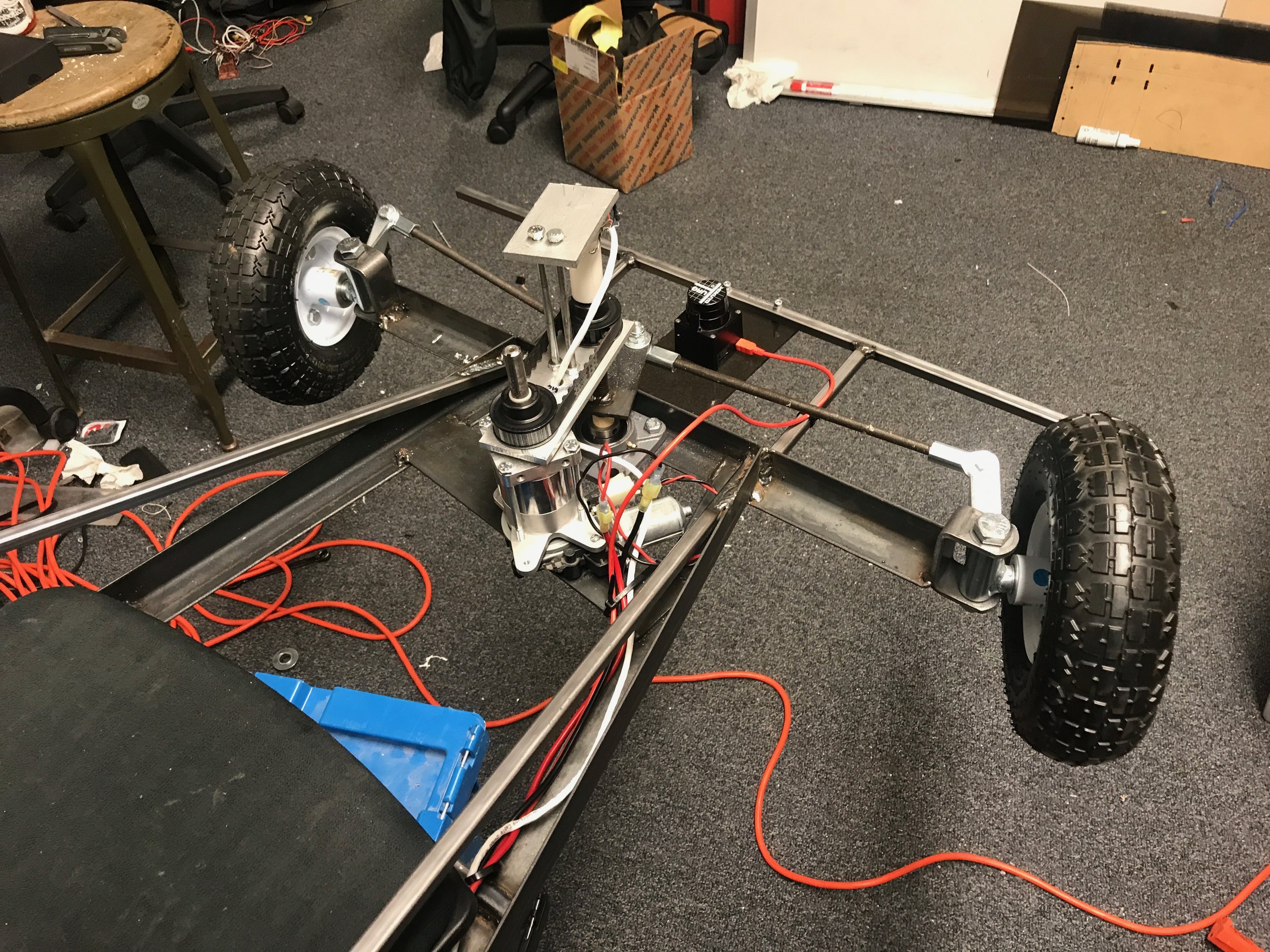
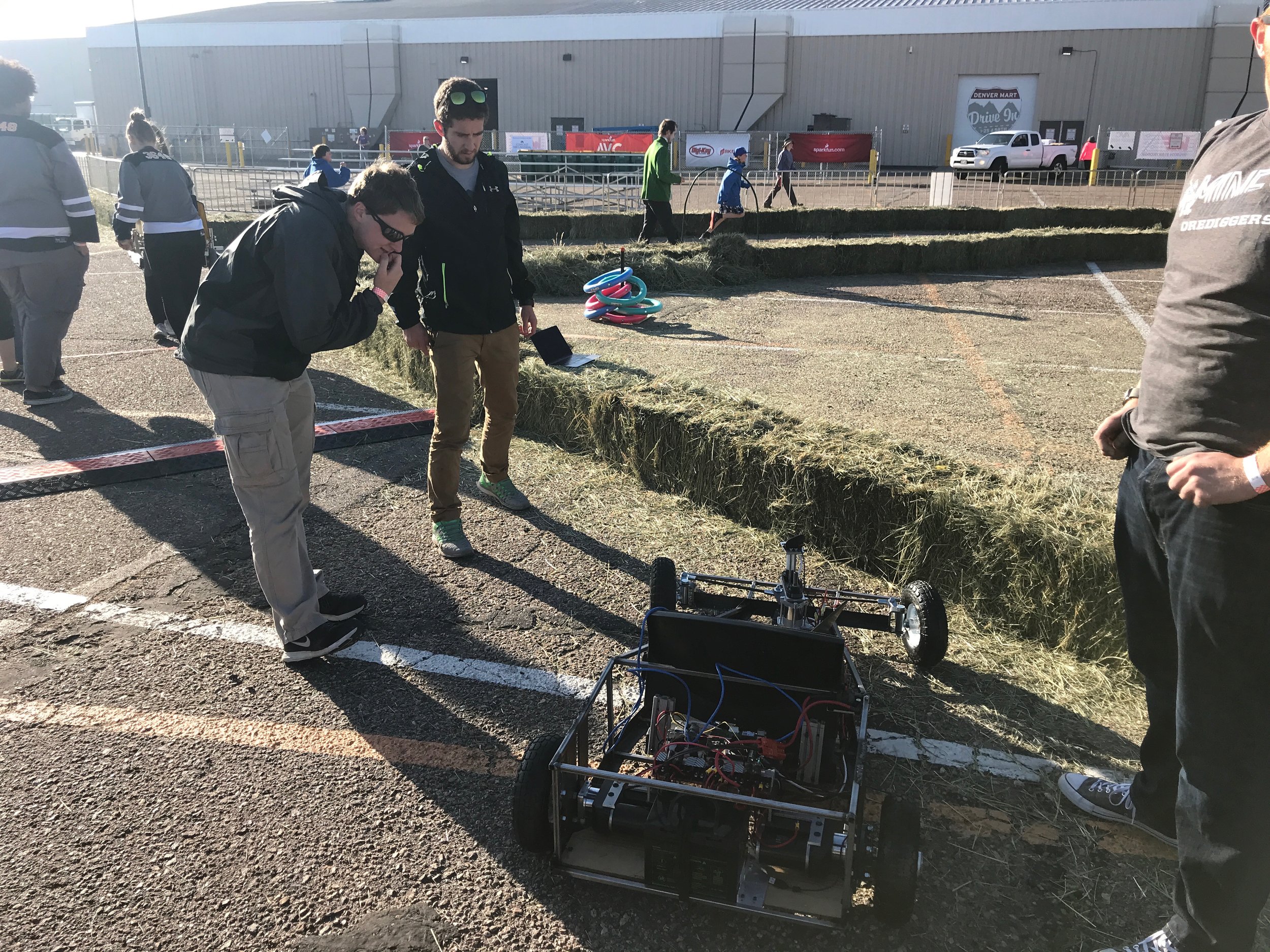
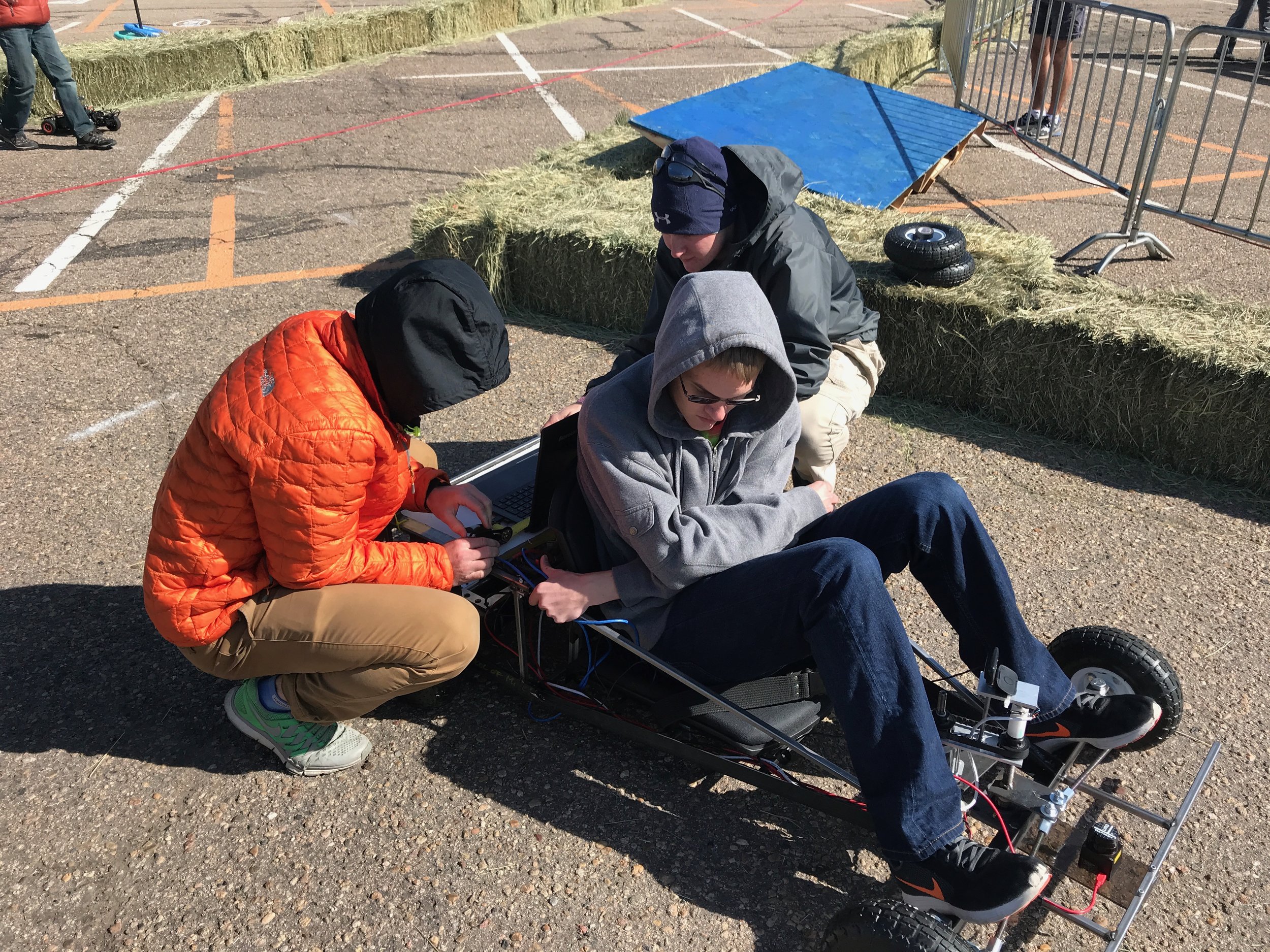
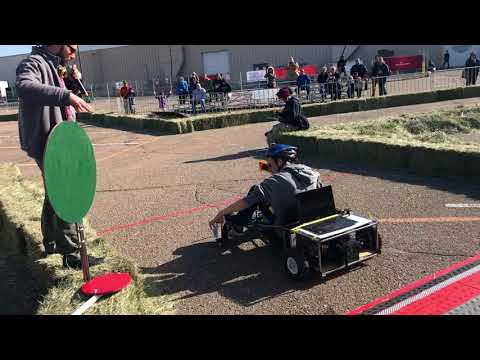
The team, lead by Sevy, started out by designing a frame and cutting out all the correct lengths of steel. Shown in the picture is the metal laid out in the orientation it will be welded. A picture of the design is in the upper left.
The welding process starts.
The mostly finished frame.
The steering mechanism: The particular sub-system above took a week to put together. A problem the team solved along the way was the motor did not have enough torque to steer the wheels. They added a planetary 12:1 gearbox on top to give it less speed and more strength to overcome this problem.
A steering arm and wheel are attached to a spindle that rotates on a bracket welded to the frame.
This was the initial drive train system. It consisted of a timing belt connecting a motor gearbox to a main drive shaft.
Sevy is running the motor and applying resistance to the wheel to simulate it on the ground. He does not like the sound it is making. Also notice how the motor wobbles. That is also a big problem.
At this point the team decided to do direct drive from the motors to the wheels and bypass the timing pulleys and belts. This is one member of the team turning a part on the lathe that will become a spacer between the drive shaft and the main bearing attached to the frame (pillow block). Normally one never goes directly from motor to wheel (direct drive) but the robot was due at competition the following day. Everyone agreed the direct drive would be the most likely to function.
In this shot, one member of the team is programing the autonomy code that will be later used to control the wheels and steering.
Direct drive! Amazingly, it functions.
The steering sub-system is all wired up.
Testing out autonomous code at the competition. The team used LIDAR as their main sensing apparatus. It could look forward and identify the direction and distance of the hay-bails.
Making some last minute touches before the AVC Sparkfun Autonomous Car Wars Competition.
The car successfully runs and steers with a person riding it after only seven weeks. However, the autonomous code as you see above needs some more time and labor. Overall the team and Sevy learned a great deal from mechanical car subsystems to time management at the extreme.